Dampers
Dampers continuously transform energy introduced into the structure during the seismic event into heat. This prevents structural accelerations and displacements from exceeded design limits and avoids damage. The damping property of different materials and fluids is utilized for this purpose. There is a choice of deformation and velocity dependent systems as well as adaptive systems.
As a rule, dampers are used in addition to conventional or isolator systems in order to increase damping effectively and achieve restraint or at least obtain greater rigidity in service load cases.
MAURER hydraulic dampers: MHD
MAURER hysteresis dampers: SHARK®
MAURER dampers | MHD | SHARK® |
Specified in accordance with | EN 15129 or other | EN 15129 or other |
Type of function | velocity-dependent | displacement-dependent |
Loads | < 10 MN | < 2.6 MN |
Displacement capacity | ++++ | ++ |
Energy absorption | ++++ | +++ |
Temperature | -50° to +80°C | -40° to +50°C |
Size | medium | medium – large |
Service life | >50 years | >50 years |
Hydraulic dampers - MHD
MAURER hydraulic dampers dissipate energy by compressing fluid through orifices or valves under high pressure. When an earthquake occurs, an optimised fluid flow system allows relative motion and, if required, restricts the response force to a defined maximum level of choice. The velocity-dependent response force can be adjusted using any desired damping exponents (α = 0.04-2.0) to meet the structural requirements on a very individual basis.
- Force limiting possible with a special valve system
- Imperceptible resistance during thermal motion of less than 3% nominal response force
- No leakage thanks to a triple sealing system and pressure limiting system
- Hybrid solutions of fuse function or lock-up function and damping function possible
- Blocking function possible from 0.1-0.5 mm/s
- Rapid response force due to high internal fluid rigidity
- Regular maintenance not necessary in normal operation
- Operating range: -50°C to +80°C
- If the fluid heats up, this does not cause an increase in internal pressure.
- CE marking available
MHD, standard design with a joint at both ends
In the event of an extremely severe earthquake, hydraulic dampers are used concurrently with the isolators. They are usually articulated between the isolation layers. This means they can accommodate very large horizontal motion of ± 1.1 m or over in all directions.
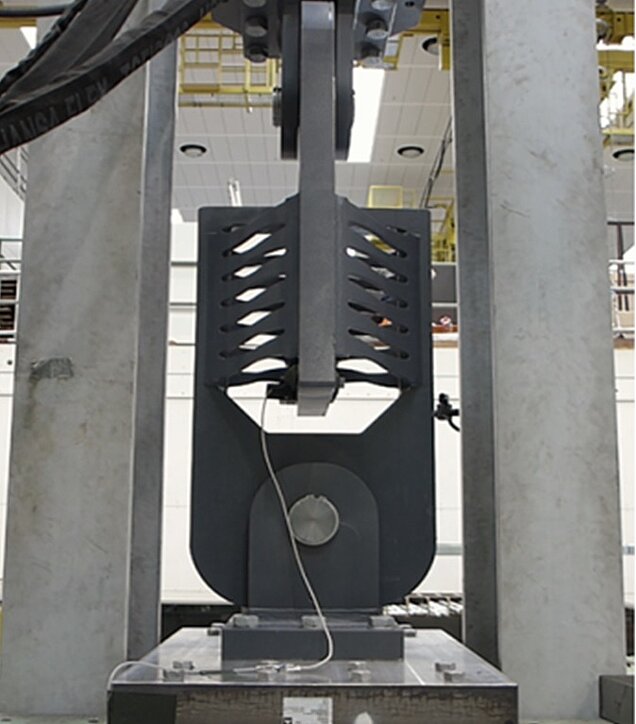
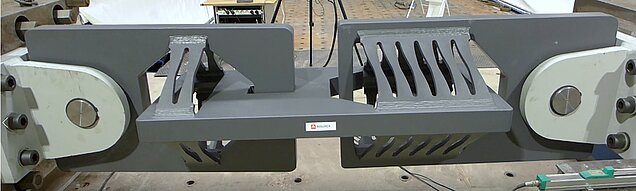
Steel hysteresis dampers - SHARK®
Plastic deformation of steel is one of the most effective mechanisms for dissipating energy, both from an economical and from a technical aspect.
- Good reliability and ageing resistance
- Functionality irrespective of temperature and velocity
- Maintenance-free
- Limited costs
- Limited capability when there is large and frequently small motion
- Service life > 100 years
- CE marking available
The SHARK® functions as a high-performance bilinear hysteresis damper. Energy dissipation is produced by a series of steel blades that are aligned accordingly on the four surfaces in the core section. The damper is designed for major earthquakes and provides reliable, stable dissipation of energy.
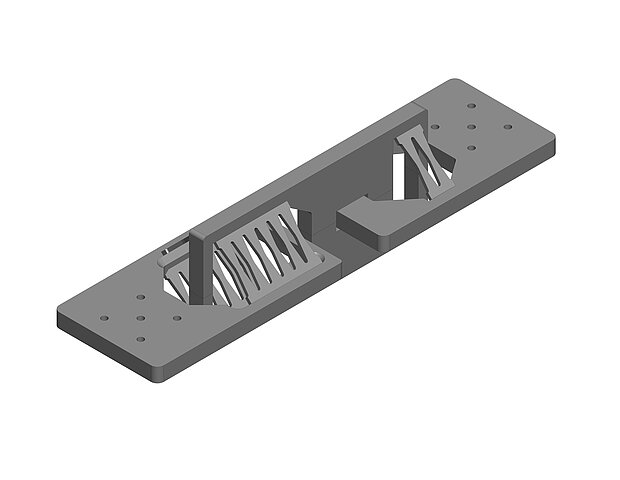
- Regular maintenance not necessary
- Consistent performance as there is no ageing
- Stable reaction in 3-4 MCE seismic events without damage
- Redundant reliability thanks to parallel arrangement of the steel blades
- Simple bilinear model for analysis
- Compact size
- Simple visual inspection, and if necessary, after a fire or other unforeseen events
Temporary restraint systems – MSTU/MSTL Shock Transmission Unit
Restraint systems can also be designed so that horizontal thermal motion is possible without resistance and that motion is only stopped in the event of corresponding shock or pulse loads. These devices are hydraulic and are called shock transmitters.
In conformance with EN 15129, the design force should be increased with a reliability factor γx of 1.5, unless an overload protection system (load limitation) is used, in which case the factor may be reduced to 1.15. In the event of sudden service or seismic impact, the restraint systems with load limiters, called MSTL, can be connected in serial and parallel arrangement. This distributes the loads evenly. The restraint systems without load limiters, called MSTU, can also be used in serial or parallel arrangement. However, possible overload needs to be taken into account in the preliminary design with a reliability factor γx of 1.5. This is why the MSTUs are larger and more expensive than MSTLs. What is more, the structure must be designed for greater forces, in which case the MSTL version with load limiters is the better choice.